Laser cleaning technology has emerged as a superior alternative to traditional chemical methods for automotive coating removal. This technology is not only highly efficient but also precise, environmentally friendly, and cost-effective. Our company currently offers two main types of laser cleaning equipment: the HCC series laser rust cleaning machine and the HCP series laser cleaning machine. Below, we will delve into the specifics of laser ablation coating removal technology.
Laser Ablation Coating Removal Technology
Laser cleaning machines are extensively used in the new energy vehicle sector, particularly for lithium battery components. The process involves removing coatings from battery cores, cleaning electrodes, pole pieces, cover plates, foil, and other small parts, necessitating high precision and refinement. For this reason, pulse laser cleaning machines are predominantly used in the automotive industry. Our pulse laser cleaning machines come in various power levels: 50W, 100W, 200W, 300W, and 500W. These machines are designed to cause minimal to no damage to the base components, making them ideal for the precise requirements of battery cell coating removal.
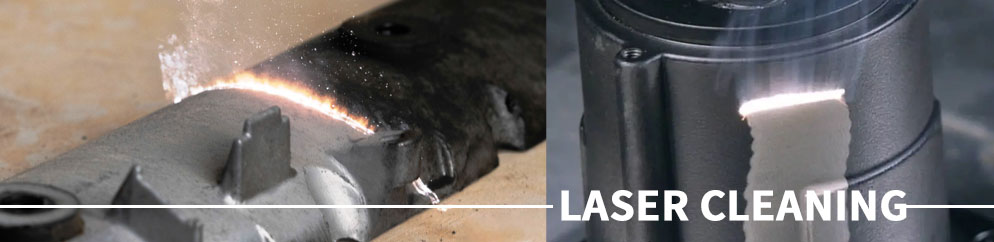
Laser cleaning is defined as the process of removing unwanted substances or contaminants from solid substrates. This includes removing foreign organic impurities or coatings from solid or metal surfaces. The advantages of laser cleaning over traditional wet chemical methods are numerous, including its universality, precision, controllability, selectivity, and environmental friendliness. Laser ablation, a mechanical process achieved through high-intensity pulsed and continuous laser irradiation, offers several benefits. These include non-contact cleaning, in-place cleaning, rapid processing times, the elimination of toxic solvents, preservation of the metal substrate, and controllable cleaning parameters.
Applications in the Automotive Industry
Laser Cleaning of Metal Foil Parts
In lithium batteries, the positive and negative electrode pieces are created by coating aluminum and copper foil with respective materials. Ensuring the cleanliness of these foils is crucial to battery safety. Contaminants can cause micro-short circuits, leading to potential fires or explosions. Traditional ultrasonic cleaning methods, which use ethanol solutions, have limitations such as causing fine holes in aluminum foil due to the cavitation effect. This is particularly problematic for thin foils used in battery electrodes, which are prone to tearing and damage. Laser ablation technology, however, can enhance cleaning efficiency, save resources, and enable real-time monitoring of the cleaning process. This improves the consistency of electrode batch production without damaging the foil.
Cell Lug Laser Cleaning
The cell lugs, which are the metal strips that draw the positive and negative electrodes out of the battery, must be free of contaminants to ensure reliable and durable electrical connections. Contaminants like grease and corrosion inhibitors can lead to poor weld quality, resulting in lower conductivity and compromised battery performance. Manual, wet flow, and plasma cleaning methods have various shortcomings. Laser cleaning technology can significantly improve this process by ensuring a clean surface, thus enhancing the strength and reliability of the welds.
Advantages of Laser Cleaning in Battery Cell Manufacturing
1. Efficiency: Laser cleaning machines can quickly and effectively clean battery cell components without damaging electrode plates, separators, or other parts. They are more efficient, precise, and safe compared to traditional methods.
2. Precision: The ability to adjust laser intensity and focus allows for fine processing of battery component surfaces, ensuring cleanliness and smoothness, which improves battery performance and lifespan.
3. Environmental Protection: Laser cleaning eliminates the need for chemical cleaning agents and water, preventing environmental pollution. It also allows for non-destructive cleaning, reducing environmental harm from waste batteries.
4. Low Cost: Laser cleaning machines reduce manufacturing costs by lowering operating and maintenance expenses, as well as reducing energy consumption and material waste in the battery manufacturing process.
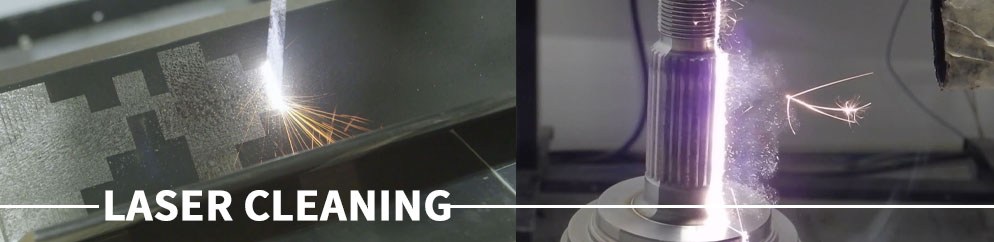
Mechanisms and Development Focus
Laser coating removal involves thermal ablation, mechanical effects, or a combination of both, depending on the laser beam characteristics and delivery method. Our development focuses on optimizing the coating removal process to minimize substrate damage, reduce health and environmental impacts, and lower labor costs. We are committed to addressing these concerns through continuous improvement and innovation in our laser cleaning technology.
By leveraging laser ablation coating removal technology, our company aims to provide the automotive industry with a highly efficient, precise, and environmentally friendly solution for coating removal, ensuring better quality and performance in battery manufacturing.
由用户整理投稿发布,不代表本站观点及立场,仅供交流学习之用,如涉及版权等问题,请随时联系我们(yangmei@bjjcz.com),我们将在第一时间给予处理。